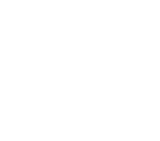
2019
A lot of time was spent sanding and polishing the aluminium beadings. They were all sent to the anodisers to get the old anodising stripped off and then the laborious process started. They ended up not quite have the lustre of anodised beadings, but the results were nevertheless good. These would have to be polished by hand with Autosol every now and again, depending on exposure to the elements.
The air vent grill took almost a day to sand and polish, but the result was good.

The rear windscreen was fitted, and the beadings replaced, as well as the quarter windows on the rear doors. Of all the seals on a W108/9, the rear quarter windows seals are the only ones no longer available and won’t be re-produced again, so they quarter windows went back with the old seals. The glass was not replaced with polycarbonate because of the risk of breaking the seals in the process.
The side glazing was sent to a supplier to make windows from Perspex. He matched the tint colour and then bent them to the correct profile using the glass windows as moulds. These were then fitted with new window channels. The windows would not be working, so brackets were made and zinc plated to secure them in the channels, which are shorter than normal and purely in place for aesthetics.


_edited.jpg)
_edited.jpg)
_edited.jpg)
The task of cleaning the grill was being avoided but eventually had to be done. It was time consuming polishing every hole with a toothbrush, but the result was good.


The grill surround had been re-chromed but when it came to reassembly, the horizontal beadings were incorrectly supplied – they were for a Fintail. The correct beadings finally arrived, and the grill was reassembled and installed.
_edited.jpg)
All the wood trim that had been sent away for restoration finally arrived back. The dashboard wood was replaced along with the top dashboard cover and lower dashboard cover. Everything went together quite nicely and relatively easily. The original dashboard was cracked, so it was upholstered in leather, but the reverse side to give a suede look, like on period racing cars. Suede dashboards on racing cars was a practical solution to prevent reflection of the dashboard onto the inside of the windscreen.
_edited.jpg)
_edited.jpg)
_edited.jpg)
Because the key ignition switch was no longer going to be used, a blanking plate was made from aluminium, which was polished and glued onto the trim surround and then fitted back in place.


The windscreen got fitted and the advice given was that the windscreen beading needed to be fitted into the seal first, then the seal mounted onto the windscreen after which the whole thing could be installed. The windscreen is bent Perspex, which is a bit floppy so there was no way that any of this would stay together. The windscreen went in easily enough – no more than a ten-minute job, but fitting the beading was a chore. Nevertheless, it finally came together.
_edited_edited.jpg)
Before the windscreen was fitted, the wood trim on the inside of the windscreen was removed so that it wouldn’t get damaged. On trying to refit the wood once the windscreen was in place, the wood wouldn’t go in because the roll cage was in the way. There was absolutely no way that the windscreen was going to be taken out again, so the only solution was to cut the trim in half – this being a recently and expensively re-veneered piece of wood. The cut was made and with a bit of filing and fettling the result turned out well with the cut noticeable, but neat.
_edited.jpg)

_edited.jpg)
When the door panels came back from upholstery, the stitching at the bottom of the panel was not up to scratch – the stitching was skew to say the least.

To remedy this, the door panels were unpicked up to the stitching. Aluminium strips 3mm thick were used to re-cover the bottom of the door panels with the reverse side of the leather for a suede look.



The panels were all fitted along with the wood trim surrounding the windows. The door handles and the windowsills were the original mushroom colour items that were professionally re-painted black to match the colour of the black leather.
_edited.jpg)
The leather on the steering wheel looked a bit worse for wear, so the steering wheel assembly was stripped down. The steering wheel boss was sent for powder coating and the steering wheel to be recovered.

Once everything came back, some new leather-look vinyl was bought to recover the steering boss adapter and then everything was reassembled.

_edited.jpg)
_edited.jpg)
The novelty of polishing the aluminium beadings wore off a long time ago, but the beadings below the windscreen and the gutter beadings still needed to be done. After putting this off for a while, it finally got done and fitted.
_edited.jpg)
_edited.jpg)
The original seat bases of car were retained, which offers length and height adjustment. These had fifty years of old grease and grime packed on, so the bases were taken apart, powder coated, and the rails and adjustment levers zinc plated. The plastic handles did not react well to the acid during zinc plating, so the handles needed to be painted.


Despite all the photos taken, re-assembling the driver’s side seat base proved to be a bit of a puzzle, but it did eventually get reassembled.



_edited.jpg)
_edited.jpg)
_edited.jpg)
_edited_edited.jpg)
The gearshift mechanism was a bit tired, so it was overhauled with new rubber bushes and the gear links were plated. The gear lever was polished up and chromed.


The switch panel that had been made a few years previously was finished by being completely welded, fettled and then sanded. It was painted in a black crackle finish for a period look.



Finally, all the switches were fitted, along with a neat little seal around the opening for the wiring harness. The labelling was done in Dymo tape for that real period look, and of course all labels were made in German
_edited.jpg)
_edited.jpg)
The switch panel was secured in place and a leather gear lever gaiter was fitted.
_edited.jpg)
When it came to re-fitting the brake cooling ducts, it was decided that the brackets made previously were just too heavy. They were made from 20x3mm flat bar, so new brackets were made using 19x2mm flat bar and once plated, the saving was almost 1kg.

_edited.jpg)
_edited.jpg)
The tank was fitted and secured in place with a strap. The filler was modified to align with the fuel tank, and breather pipes were added. Once done, it was sent for powder coating and then the top part of the filler was painted in red to match the colour of the car.
_edited.jpg)


_edited.jpg)
%2520-%2520Copy_edit.jpg)
_edited.jpg)
A breather pipe was made, plated and then fitted to the top of the tank. This was connected to the breather pipes on the filler with rubber hoses and clamps.
_edited.jpg)
_edited.jpg)
The taillight reflectors were sent away to get metalized and the backs were painted.
_edited.jpg)
_edited.jpg)
The wiring harness for the car had been installed, but everything still needed to be connected and tested. This happened over a few weekends and there were a few gremlins to be sorted out. Once everything was tested, the harness was secured in place.

The car was now effectively finished except for a few detailed things but work on the engine had been going on in the background.
All the relevant nuts, bolts and washers for the entire engine were zinc plated, and the various ancillaries were overhauled, like the air suspension compressor and power steering pump unit, oil filter housing, distributor and water pump. The water pump was sent away to be restored and came back with a new impellor, bearings and seals.
_edited.jpg)
_edited.jpg)
_edited.jpg)


The inlet manifolds were stripped down and bead blasted, then reassembled with new gaskets and seals.
_edited.jpg)
_edited.jpg)
_edited.jpg)
_edited.jpg)
Some of the Bakelite spacers for the fuel injector mountings were broken and badly repaired, so new ones were machined as they are no longer available new.
Some extensive modification was done to the original clutch setup. Initially a new flywheel was turned to accommodate a Mercedes Sprinter clutch and pressure plate, but it was decided that this would not last for too long, so a new, considerably lighter, flywheel was turned.
_edited.jpg)
A proper racing clutch pack made in the US was installed that is used on most of the local racing American V8s – good for 1000hp.
_edited.jpg)

The clutch discs are sintered copper and the whole arrangement is a thing of beauty. The weight saving was a massive 50kg! Sad that it will all be covered up.


During the second track test before the car was stripped down for paint, the clutch failed – the pivot pin for the clutch fork had broken. It turned out that the whole arrangement was too far forward, so a new solution was found and a concentric thrust bearing was modified to fit. This did away with the original clutch fork and pivot pin arrangement.

The block was sent to be bored, taking the cylinder diameter from a standard 102mm to 107mm. Once returned, the block was painted.
_edited.jpg)
_edited.jpg)
New inlet and exhaust valves, which took three months to manufacture, were made in the UK, with the stems being slightly thinner and the inlet valve diameter being increased from 49mm to 51mm. The cylinder heads were sent away to be ported and polished by an old retired tradesman and was beautifully done. The new valve seats were made and fitted, but the corrosion from the cooling system was quite severe. The holes were welded up and re-drilled slightly off-centre to make allowance for the larger cylinder bore.


The crankshaft was polished and was balanced along with the new flywheel and clutch assembly.


