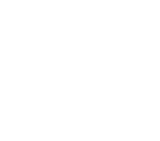
2018
Eventually it got to the point where car could be stripped down entirely to send it for painting - everything was bagged and labelled, and hundreds of photos were taken to ensure that everything would go back in place again.
_edited.jpg)

_edited.jpg)
_edited.jpg)
Before being sent for paint, the grills to cover the air vents on the bulkhead for the under-bonnet heat extraction system were made.
A template was made from cardboard which was traced onto a steel sheet that was then cut out. Two of these were made for each side and the fly screen material was clamped between the steel frames. The left-hand side grill was a bit more complex and needed some bending to follow the shape of the bulkhead. The steel frames were zinc plated much later.









All the wood was sent for re-furbishing along with the chrome and the next few weekends were spent making a trolley to be able to move the car around to get it to the paint shop.
_edited.jpg)

Quite a lot of time was initially spent by the spray painter to remove the sound deadening material from inside the car, as well as all the oil and grease from under the car. Within two weeks the car already looked transformed.






While the car was away, work started to on the engine and this was duly stripped down.

_edited.jpg)

_edited.jpg)

The engine was sent into the engineers who reported that it was in good condition. The crankshaft would only need to be polished and the bores were also okay, but it was going to be re-bored anyway to accommodate 107mm diameter pistons for a 450SEL 6.9 that were sourced from the USA.
The next four or five weekends were spent tackling the wiring harness, which was laid out on a worktable. The car had to be re-wired because a lot of the wires in the engine compartment were hard and brittle, like those running from the alternator. Also, a lot of unnecessary wiring was removed that fed things like the electric windows, interior fans, door/light switches and so on.
With the help of a very good friend who is an auto electrician, the loom was restored. Existing wires that were still in good condition were still used and additional wiring was added, like for the spotlights. All the sleeving was replaced, and new electrical plug connectors were ordered that were missing, like on the alternator where modern spade connectors had been used. All the original plugs were used, but they had to be removed to fit the new sleeving. Each plug was removed, photographed, bagged and labelled to ensure that everything went back correctly. A new grommet that seals the loom into the firewall was ordered and fitted
_edited.jpg)
Eventually the wiring harness was completed and ready for installation. Some wires were left longer, and the plugs left off to be cut to size once everything was in place.


The items sent for re-chroming were returned, but some items were sent back because the quality was not up to scratch.
The door handles were re-assembled where the relevant metal parts were zinc plated and fitted - at the end of the day the door handle parts are behind a door panel and nobody will notice if they're dirty or rusty, but the devil is in the detail.

The paint work on the car was completed and the result was spectacular.
_edited.jpg)
_edited.jpg)
_edited.jpg)

_edited.jpg)


_edited.jpg)
_edited.jpg)
Once the car was collected, work started in earnest to re-assemble the car. The headlight units were restored and fitted with new main beam units. The bezels were re-chromed and new park lights and indicator lenses were fitted. The old headlights at the top were retained, but covered in black vinyl, as per the original car.
_edited.jpg)
_edited.jpg)

_edited.jpg)

_edited.jpg)

Small things that make the biggest difference were done, like fitting the taillights and boot lid badges. The side lights which illuminate the number sticker at night were sourced from a local parts centre but were first powder coated black before being installed. The re-chromed window frames for the doors were fitted, along with the doors locks and strikers, which were also zinc plated.
_edited.jpg)
_edited.jpg)
The wiring harness was fitted only to find that the grommet in the firewall was the wrong part – it was too big, so nothing could be connected until the correct grommet was found. This would have to be pushed in from the longest point, i.e. the right headlight.
In the meantime, the pedal box was disassembled, powder coated, re-plated and refitted.


The brake booster was re-painted, the aluminium spacer sand blasted and reassembled into the car with a repainted brake master cylinder. The air suspension distribution valve was overhauled, sand blasted, connectors re-plated and refitted with a new control cable. The wiper motor was painted, plated and installed.

_edited.jpg)


The steering column was repainted and temporarily fitted so that the brake/ air pipes could be routed. All the brake and air pipes were sent for plating but came back out of shape - they had been bent to get them into the plating tank. Bending them back into shape and refitting them was challenging and really time consuming. Securing brackets were re-plated and new mounting rubbers installed. The rear bellows were cleaned up and installed - these were refurbished some time ago already. The dark yellow zinc plating was not ideal, but it would fade over time to a lighter, more normal colour.

_edited.jpg)

The front quarter lites were replaced with poly carbonate windows cut from a 5mm sheet and inserted with the original securing seals into newly chromed frames. These were re-assembled with new window seals and re-fitted. They are indistinguishable from the original glass windows



The trim beadings were a source of concern as most of them have scuffs and scratches. A sample piece was sent in to get re-anodised, but it was not as shiny as the original. Like any other surface treatment, the final product is only as good as the preparation, so a polisher was bought, the old anodising was stripped off and a few hours was spent polishing the rear windscreen beadings. It started with 220 grit water paper to get the scratches out, then 400, 800, 1000, 1500 and finally 2000 before polishing the beadings with a green colour soap, recommended for fine polishing of copper and aluminium. The result was good, and the beadings were sent back for mirror chrome anodising.


An afternoon was spent working out the sizes and proportions of the various decals needed so that these could be made.

As seen earlier, the front suspension had already been overhauled, so it was cleaned up and refitted. All the air pipes were plated and connected.
_edited.jpg)

_edited.jpg)
The rear suspension was also cleaned up before being re-fitted.
_edited.jpg)
_edited.jpg)
_edited.jpg)

The alcohol jar was bead blasted, plated and installed.
_edited.jpg)
The auxiliary fuel pump was refitted with the fuel filter, which was also bead blasted and plated.

The original fuel pump was cleaned up and installed.
_edited.jpg)
The new grommet in the firewall for the wiring loom duly arrived and it turned out to be the same as previously ordered – it seems the part number supersedes to this new part number, which is entirely the wrong part. The grommet is a 115 part number for a 70mm hole, whereas the hole in the firewall is 40mm in diameter. A friend suggested a grommet to seal the aircon pipes on a Mercedes-Benz R107 SL.
The brake booster was removed again to re-fit the new grommet - there simply wasn’t enough space to get the grommet in without removing it. The wiring loom was dismantled taking off all the plugs to push the new grommet over, which went surprisingly easily. Once in place it was a bit loose but seems to be doing the job.


Once in place the other grommets were fitted – one for the height regulator cable, one for the clutch fluid pipe and another for the oil pressure tube. The relay bracket was fitted, and all the relevant electrical plugs were connected. The loom was positioned and secured into place with clamps and then finally the booster was installed with a new reservoir.
_edited.jpg)
_edited.jpg)
At the same time, the grommets for the ignition cut-off cable and the windscreen pump electrical cable on the other side of the engine bay were fitted.

The air tank came back from the powder coaters, was reassembled and then installed on new rubber mountings with all the relevant air pipes connected.

_edited.jpg)
The fitment of the fender and door beadings was tricky. Excluding the front doors, all the other beadings needed to be cut to accommodate the larger wheel arches. Being stainless steel, these proved difficult to cut with a hacksaw, so an angle grinder was used instead once the beading had been disassembled. It was a frustrating and time-consuming job changing the beading lengths – the end caps were glued in and needed to be cut out and then modified because the angle was opposite. The end result was good.
_edited.jpg)
_edited.jpg)
_edited.jpg)
The rear windscreen beading came back from anodising and the experiment didn’t work. The finish was cloudy and there were pitting marks. According to the anodising company, anodising old aluminium is very difficult. Contrary to belief, aluminium does oxide and it’s the oxidation that causes all the imperfections. No matter how much polishing is done, the change in the material composition over time is what causes the imperfections. New aluminium is easy to anodise with excellent results. There was no option but to get the beadings stripped of the anodising layer, and then to sand and polish them.


All the clips for the windscreen and rear windscreen beadings were zinc plated and riveted into place.
_edited.jpg)

All the decals were collected from the suppliers and the process to apply them was started. Some of the decals proved too intricate to apply, like the large number roundels on the doors, as well as the yellow ‘H.E. SIEGER’ decal. The shape was just too complex because they had to go over the beading and then stretch over the wheel arch, so the professionals were called in to do get these applied.
_edited.jpg)
_edited.jpg)
_edited.jpg)
_edited.jpg)

